聯(lián)系我們
地址:暫無
手機/微信一:15524700779
手機/微信二:13654200914
QQ客服一:暫無
QQ客服二:暫無
手機/微信一:15524700779
手機/微信二:13654200914
QQ客服一:暫無
QQ客服二:暫無
產品知識
大型建筑鋁模板型材擠壓生產對幾何尺寸影響因素及解決措施
日期:2017-10-09 人氣:
內容提示: 本文闡述了大型建筑鋁模板型材在擠壓生產中對幾何尺寸的影響因素及防控解決措施,分析了在生產過程中造成幾何尺寸不合格的關鍵因素,通過對鋁棒和擠壓工藝、擠壓參數(shù)、工!
本文闡述了大型建筑鋁模板型材在擠壓生產中對幾何尺寸的影響因素及防控解決措施,分析了在生產過程中造成幾何尺寸不合格的關鍵因素,通過對鋁棒和擠壓工藝、擠壓參數(shù)、工模具、拉伸矯直等幾種工序的要點控制,來解決擠壓時對幾何尺寸造成的影響,總結了擠壓生產大型鋁模板型材的經驗和過程控制方法。
一 概述
隨著鋁加工業(yè)的快速發(fā)展,大型擠壓機技術快速提升,生產大型鋁合金型材的能力逐漸加強,大型鋁合金型材在結構件方面替代鋼鐵材料的趨勢逐漸明顯,促使建筑鋁模板行業(yè)的快速普及,用6061合金生產的建筑鋁模板逐漸替代鋼鐵模板和木質模板,解決了以往傳統(tǒng)模板存在的一些缺陷,大大提高了施工效率和建筑物的整體精度,鋁模板的研發(fā)及施工應用,是建筑行業(yè)一次大發(fā)展,以鋁代鋼、以鋁代木是綠色建筑結構材料的未來和發(fā)展方向。
建筑結構用的鋁模板不同于建筑裝飾材料,它是整個建筑物施工的核心部件,為了提高建筑物的精度和提高建筑模板本身的使用壽命,對生產的鋁模板型材的幾何尺寸精度和力學性能要求都非常高,其形狀特點是規(guī)格多、外輪廓和斷積面大、寬厚比大、舌型比大、異形空心型材、半空心型材較多,擠壓難度系數(shù)較大,成形困難。這些因素致使幾何尺寸(波浪、扭擰、彎曲、平面間隙、尺寸、角度超差等)難以控制,本文重點探討擠壓生產中影響幾何尺寸的主要因素和防控措施,不當之處望大家批評指正。
二 幾種典型大型鋁模板的圖紙要求及合金特性
1 常用的幾種大型建筑模板圖樣及技術要求
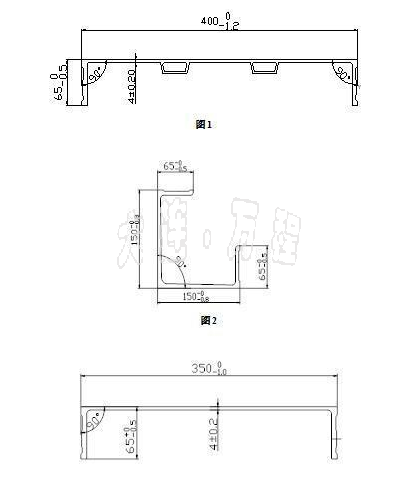
技術要求:
1、角度偏差不得超過0至-0.5°
2、扭擰度:≤0.75mm/m,L≤7m,≤4mm/L
3、彎曲度:≤0.75mm/m,L≤7m,≤4mm/L
4、平面間隙每100mm寬不得大于0.2mm,總寬度*0.2
5、韋氏硬度:≥15HW
6、壁厚偏差不得大于±0.2mm
7、公差按GB/T14846-2008超高精級執(zhí)行
2 6061合金
6061合金,具有中等強度, 合金成分中Mg和Si含量增多,以及添加少量的Cu和Cr使合金的強度增加,該合金還具有良好的塑性和優(yōu)良的耐蝕性,是生產模板的首選材料。
含有Mg2Si多的6061合金淬火敏感性高,對力學性能影響較大,含有1.4%Mg2Si的6061合金,從545°C冷卻到204°C,最小冷卻速度不應小于650°C/min,才能獲得人工時效后的較高強度。
三 難點分析及幾何尺寸變形現(xiàn)象
圖1、圖3兩種型材屬于典型的扁寬型材,其寬厚比達到了100,按理論要求必須在7500噸以上擠壓機上生產,我們最大機臺是4500T,擠壓筒直徑368mm,圖3型材的外接圓直徑幾乎和擠壓筒直徑相當,圖1型材的外接圓直徑已經大大超過了擠壓筒直徑,而且該型材中間有兩個小孔,擠壓時小模芯容易發(fā)生嚴重偏移現(xiàn)象,從而影響出料成型。要生產這兩種型材用一般的平面分流模具是達不到擠壓型材技術要求的,這就需要設計制作特殊的寬展擠壓模具才能保證型材成形及寬度和平面間隙合格。
其難度特點是極容易發(fā)生嚴重的壁厚超差和平面間隙,易出現(xiàn)寬度方向尺寸不合格,一般偏小較多。角度也出現(xiàn)偏小較多,壁厚易出現(xiàn)壁厚不夠較多,平面間隙易易出現(xiàn)凹面現(xiàn)象較多,該種型材的大面上極易出現(xiàn)波浪凹凸現(xiàn)象。
生產圖2型材時易出現(xiàn)角度不合格現(xiàn)象,該型材屬于典型的半空心大懸臂型材其生產難度有目共睹,擠壓時懸臂極易壓塌,模具極易損壞,是典型很難擠出合格型材的,難以保證尺寸精度和形位公差,角度大小變化較多,綜合尺寸難以控制。
三種型材的角度都超出了鋁擠壓材《標準》中的任何最高等級的規(guī)定,這給模具設計制造帶來了很大的難度。
四 影響幾何尺寸的幾種因素及解決措施
根據(jù)型材斷面和米重我們選擇了在4500T設備上進行生產,該設備擠壓筒直徑368mm,可實現(xiàn)快速換模,每換一套模具可節(jié)約10——20分鐘,并配備智能化數(shù)控水霧風在線淬火設備,可以實現(xiàn)在線淬火,由于鋁合金水霧風一體化在線淬火設備的廣泛的應用,提高了制品的表面質量和成品率,大大降低了人工勞動強度。
鑄錠我們采用的的是均化處理后的鑄錠,鋁棒加熱爐采用的是工頻加熱爐。
1 鋁棒影響及措施
鑄錠質量指標主要是晶粒度一級,氫含量少,渣少粒細,金相組織均勻,無裂紋、疏松、氣孔和元素偏析。這樣鑄錠的塑性和變形性好,擠壓力下降, 擠壓速度提高。否則,會導致擠壓速度慢,模具耗損也大。
因為鋁棒在鑄造生產中采用半連續(xù)鑄造方法生產,冷卻速度快產生非平衡結晶,偏離平衡結晶狀態(tài),α(Al)的固溶體中Si、Mg和Mg2Si不均勻產生晶內偏析和區(qū)內偏析,結晶過程中生成粗大的Mg2Si,F(xiàn)e和Si生成β(AlFeSi)相,這種不均勻的現(xiàn)象造成鋁棒局部抗力較大,又因為鑄造產生的內應力等因素給擠壓生成帶來了很多不利影響,擠壓時模具受力不均勻造成彈性變形,致使幾何尺寸變形較大。
所以大型斷面擠壓用的圓鑄錠是經過560°C均勻化處理后的鑄錠。以消除晶內偏析,使強化相Mg2Si充分溶解,消除鑄造產生的內應力,降低擠壓抗力,提高金屬的塑性,減少擠壓時對模具造成的變形,可以減少擠壓時幾何尺寸的變化。
2 工模具的影響及措施
大型鋁模板模具在設計時充分考慮分流孔及導流孔的分布位置,做到各部位能吸收同量的金屬,在不影響模具強度和型材表面質量的情況下盡量把分流孔做大。橋位設計時角度要合理,角度太大增加摩擦,使金屬流動變慢,角度越小金屬越容易焊合出料越快,橋位交接處盡量圓滑過渡減少焊合死角。工作帶長度要合理計算來均勻金屬流量。以減少模具的局部壓力,減少出料時幾何尺寸的變形。
在上機前模具工作帶要仔細拋光,保證平面度和垂直度,不得出現(xiàn)凹凸不平。在型材的擠壓中模具受力發(fā)生的變形,對型材幾何尺寸精度產生較大影響,模具材料在加熱到480°C左右時模具硬度降低,在受力方向上模具會產生彈性變形。為了消除或減少這種變形,我們采取模具專用仿形支持墊來增加模具抗力來減少變形,經實際測量在同等工藝條件下使用專用仿形支撐墊后可減少壁厚0.1mm以上的變形,其它各部位的幾何尺寸也有了極大的改觀,能夠保證順利擠壓生產,部分不達標的制品,通過精整工序整形后都能達到標準要求
1 擠壓工藝參數(shù)的影響及措施
6061合金變形抗力大,所以鑄錠加熱溫度應偏上限(460°C——490°C)。鋁棒加熱時要注意工頻爐的溫度監(jiān)控情況,一定要避免加熱不均勻的鋁棒上機生產,實踐經驗證明鋁棒加熱不均勻很難平穩(wěn)出料,造成較大的變形情況,甚至造成擠壓悶車現(xiàn)象,,不能順利生產而卸模。
模具溫度取440°C——460°C,模具采用的是電阻爐加熱方式,到溫后不能馬上上機生產,因為模具體積較大,容易造成表面到溫而內部溫度偏低的現(xiàn)象,這時候上機生產會造成模具斷橋現(xiàn)象致使模具立即報廢,即使能夠勉強出料也容易造成較大變形,出料不穩(wěn)定,所以模具到溫后必須保溫2小時以上方可上機生產,不過模具在爐內加熱保溫時間不能超出10小時,否則易產生模具退火現(xiàn)象,致使?蘸凸ぷ鲙Мa生斑點腐蝕現(xiàn)象,而影響模具壽命和型材的幾何尺寸和表面質量。
擠壓筒溫度為410°C—— 430°C 。擠壓筒保持一定溫度使金屬流動趨于均勻。因為擠壓筒溫度升高,使錠坯內外層溫度差減小,擠壓時金屬內外層變形抗力趨于一致,使得擠壓過程中的金屬流動均勻,減少幾何尺寸變形。
擠壓速度的選擇對幾何尺寸的合格與否非常重要,機手要根據(jù)型材的出料情況合理選擇,在保證幾何尺寸和其它工藝參數(shù)及設備能量允許的的情況下盡量選擇大的擠壓速度以提高生產率,我們一般控制在5m/min——12m/min的范圍內;擠壓速度高,鋁棒與模具內壁接觸時間短,能量傳遞來不及,有可能形成變形區(qū)內的絕熱擠壓過程,使金屬的速度越來越高,導致制品表面裂紋、拉傷、角度變化較大、表面波浪凹凸不平等缺陷, 當棒溫稍高、型材尺寸變化較大、表面不不好的情況下就要逐漸降低擠壓速度,如果速度降低過多就會影響型材的在線淬火溫度,只要幾何尺寸和淬火溫度符合工藝要求又能夠順利擠壓的情況下可繼續(xù)生產,否則換模生產。
為保證型材的力學性能,型材擠壓出口溫度應控制在510°C——540°C范圍內;6061合金淬火敏感性高,要求淬火冷卻強度大、冷卻速度快,制品出前梁后立即進行在線淬火,使溫度迅速降到150°C以下,擠壓時開啟智能化數(shù)控水霧風在線淬火設備以保證型材淬火工藝要求。
冷卻要自動或手動調節(jié)均勻,否則對型材造成,彎曲、平面間隙超標、角度變形等幾何尺寸不達標的情況發(fā)生。
1、拉伸矯直的影響及措施
拉伸矯直時型材溫度不能過高,型材的溫度降到50°C以下時才能拉伸轎直拉伸轎直,如果溫度過高就拉伸轎直,當型材冷卻后會出現(xiàn)較大程度的彎曲變形。
拉伸矯直時在拉伸機鉗口和型材之間使用相應專用夾具和專用墊,對型材做好支撐,減少頭尾的變形長度。特別是一些大懸壁型材及空心型材,如果不用專用墊直接用鉗口夾住拉伸,會導致型材頭尾變形量過大,而在成品鋸切時,變形部分必須切掉。這樣就造成了成品率下降,廢料太多的現(xiàn)象。 對于懸壁較長又有封閉截面的型材,矯直時在封閉腔內塞入專用墊還要在懸壁部分放支撐架,從而減少長度方向的變形量。
夾具和專用墊由專人設計,專人管理,并指導工人使用, 同時為防止工人因嫌麻煩而不愿意使用專用夾具和專用墊的現(xiàn)象,建立了成品率與工資掛鉤的獎懲機制,加強工人的質量意識。
拉伸矯直是保證型材幾何尺寸是否合格的關鍵環(huán)節(jié),拉伸時注意拉伸力的合理控制,拉力不可太大,只要能保證制品彎曲度、扭擰度符合要求就可以。拉力太大會造成平面間隙、角度等幾何尺寸不合格現(xiàn)象,但是拉力太小會影響制品時效后的力學性能特別是屈服強度,拉伸率過小會導致屈服強度偏低現(xiàn)象,實踐證明拉伸率應控制在1%——2%之間較為合適。
五 結論
1、在大型鋁模板生產過程中必須控制好鋁棒質量、工藝溫度、擠壓速度、冷卻速度、控制好拉伸矯直等各工序才能保證產品的幾何尺寸和力學性能。
2、經過以上的控制,生產的鋁模板型材的幾何尺寸已經達到圖紙要求,部分稍微變形超標的制品,通過精整工序整形后都能達到標準要求。
3、擠壓超大型材必須結合設備情況和型材的斷面特征制定可行的擠壓生產方案,并通過實踐不斷進行總結和完善,就可以掌握生產超大型材的技術。
參考文獻
[1] 羅蘇,吳錫坤.《鋁型材加工實用技術手冊》中南大學出版社,2006年6月第1版.
[2] 肖亞慶,謝水生,劉靜安等. 《鋁加工技術實用手冊》冶金工業(yè)出版社,2005.
[3] 《GB/T14846-2008鋁及鋁合金擠壓型材尺寸偏差》.
讀完這篇文章后,您心情如何?
上一篇:如何正確挑選鋁扣板